The automatic roll filters performance offer many advantages, one of all: its compact size in the autonomy of operation function. In fact, the spaces required for lodging the filter media rolls can vary from 20% for small filters to 10% for big filters of the total filter surface. This technical conception is due to its rational mechanical construction and to the compressibility characteristics of the employed filter media that allows to realize rolls with reduced diameters but in the same time with maximum uniwindings to ensure a long autonomy of operation even at hard working conditions.
Construction
The automatic roll filter produced by Filtrotecnica is completely made of pressed and bent galvanized steel sheet. All the part are assembled by steel bolts and rivets. The filter is generally furnished completely assembled in the factory ready for installation in duct or plenum. On request the filter can be supplied in a few pre – assembled components for transport or final plant reasons. The filtering media is composed of glass fibers, normally with dust binding agent, or of synthetic fibers wound on a spool and enclosed in the top section of the filter with protective cover. The movement of the filter media downward is given by a motor reducer located in the frontal bottom part of the filter in order to assemble the proper number of sections and to make checking and service operations easier. In the lower part is located the disposable spool on which the dirty media is rolled automatically.Dimensions
The automatic roll filter is manufactured in twelve standard widths: 540 – 690 – 835 – 985 – 1140 – 1295 – 1450 – 1595 – 1740 – 1830 – 2000 – 2130 mm with minimum height of 1000 mm and increments of 100 mm to the maximum height of 5000 mm On request different dimensions can be available.Installation
The automatic roll filter is normally supplied completely assembled, if it is supplied not assembled the equipment can be easily erected on site following Filtrotecnica instructions. First of all arrange in advance a level floor, set – up the sections and bolting them together and to the plenum or to the filter housing with perimetric flanges considering that a free space of at least 800 mm is desirable for servicing operation. At the end connect the control box to the drive motor and to the electrical supply. The filter can be installed with direction of air flow direct Mod. FRA (rolls of filter media upstream) or reverse Mod. FRI (rolls of filter media downstream with a complete cover for dirty roll). The filter in a single unit can also be installed horizontally keeping always the filtering section normal to the air crossing direction In this case the filter is supplied with chain tightener and twin rack.Some special versions can be supplied on request as: Mod. FRM completely cased ready to be used for duct installation or on air handling units. Mod. FRT is similar to Mod. FRA but with an additional frame holding the single counter frames of bag filters or rigid pockets filters to obtain compact high efficiency filtering unit.
Principle of operation
The air is achieved by viscous impingment principle due to the filter media that is normally impregnated with adesive oil. When the filter media reachs a pre- etted value of pressure drop a pressure switch through an electrical circuit gives to the drive motor the input to operate unwonding a new part of media till to reach a lower value of pressure drop. Two side channels guide the filter media during the uncoiling. In addition a metallic support grid, mounted on the air leaving side, prevent any media deformation or flexing caused by the crossing air pressure. These important features ensure air – tight seal between the frame and the filter media.Control
As already written in the standard application the drive motor is actuated by a differential pressure switch. In some cases, in accordance with the working installation, an adjustable timer can be provided in place of a pressure switch. Therefore the electrical control board of the electric gear motor can be supplied in two versions: the first, standard with pressure switch control, the second, on request, with timer control. To make the working and service operations easier the electrical board is provided with manual stop and feed media manual control. A switch stops the electric motor avoiding the complete roll unwounding preventing therefore the plant system from working without filter media, while a signal light appears on the control board.
Automatic Roll Filters
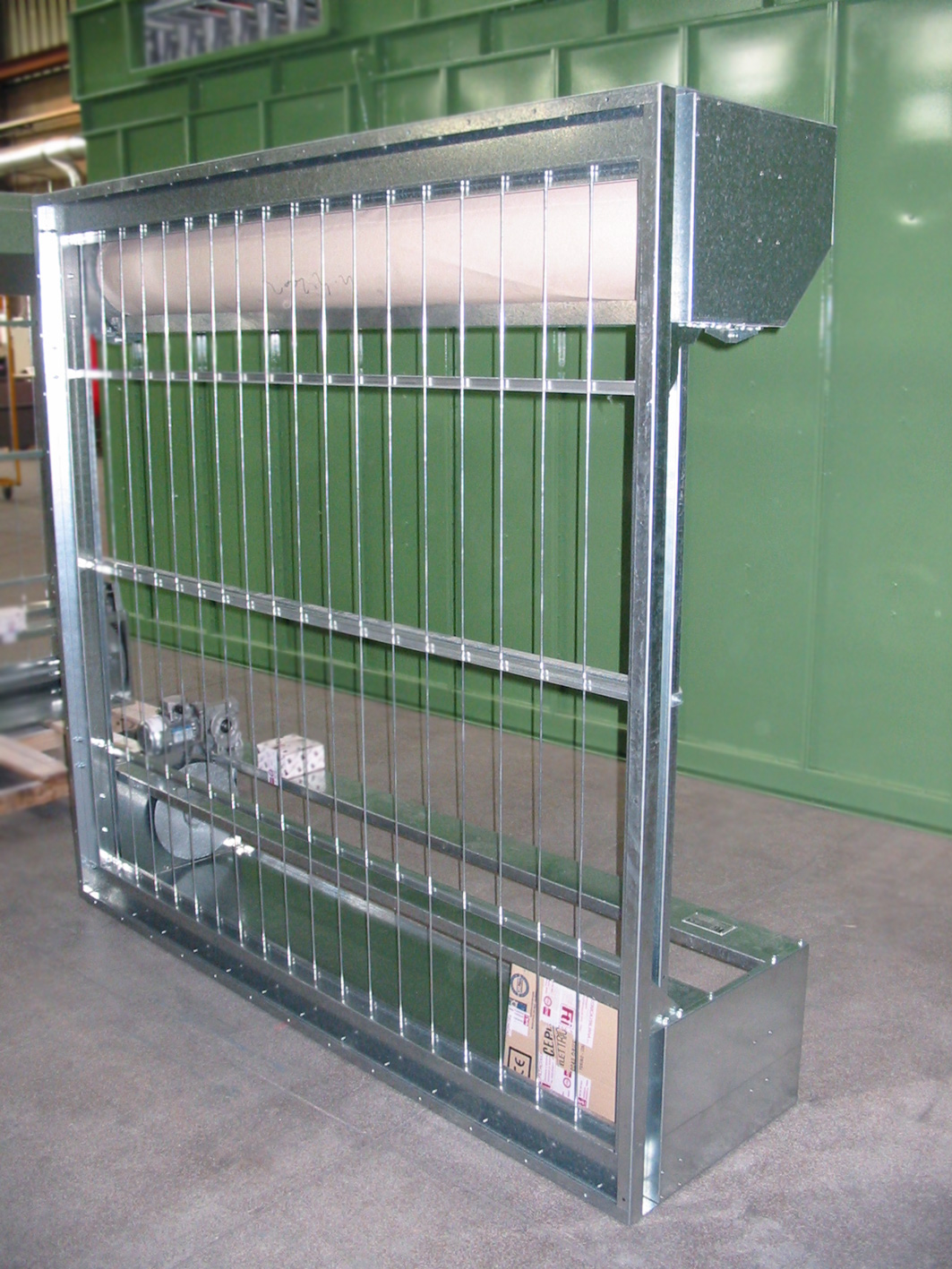